A Comprehensive Overview to Identifying, Preventing, and Dealing With Undercut Welding Issues in Your Welding Projects
In the world of welding, experiencing undercut issues is a common challenge that can endanger the architectural stability and overall top quality of your welding projects. Recognizing the origin triggers behind undercut welding, having the ability to precisely spot it in your welds, and executing efficient preventative steps are crucial abilities for any welder. Additionally, having the knowledge and methods to correct undercut troubles when they do happen can make a significant difference in the last result of your welding endeavors. Remain tuned as we discover the essential components of identifying, protecting against, and dealing with undercut welding problems, providing you with beneficial understandings and techniques to elevate your welding skills to the following degree.
Usual Reasons For Undercut Welding
Undercut welding, a common issue in welding procedures, can be brought on by various variables that need to be thoroughly determined and addressed to make sure the integrity of the weld joint. Among the primary sources of undercut welding is too much warm input. When the welding parameters, such as voltage, current, or take a trip speed, are not properly established, a too much quantity of warmth can be created. This excess warmth causes the melting and succeeding elimination of the base material along the edges of the weld joint, creating a groove recognized as undercut.
One more common reason for undercut welding is improper welding strategy. Poor manipulation of the soldering iron or weapon, inaccurate angle or range in between the torch and the workpiece, or inconsistent travel speed can all contribute to the formation of undercut. Additionally, making use of the incorrect welding consumables or electrode dimension for a certain joint configuration can bring about undercut issues. Recognizing these origin and executing corrective procedures is vital in stopping and fixing undercut welding problems in welding jobs.
Identifying Undercut in Welds
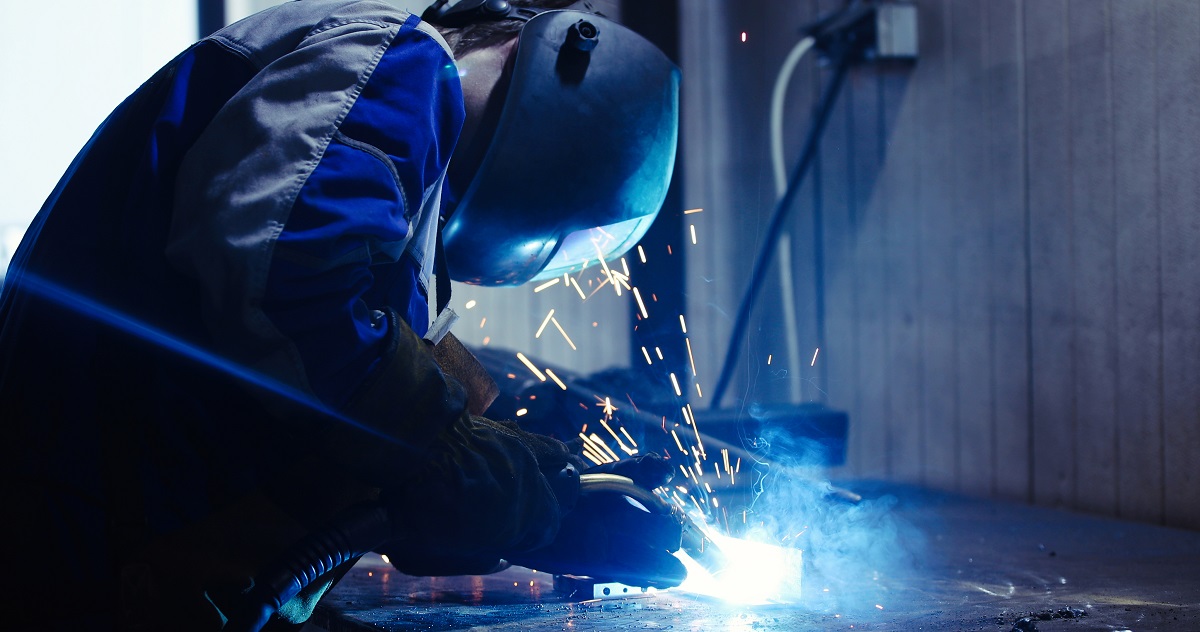
To recognize undercut properly, proper lights and magnification tools are vital to examine the weld joint extensively. Making use of tools such as a welding scale or a magnifying glass can assist in detecting even the tiniest undercut imperfections. Additionally, running a finger or a fingernail along the weld joint can in some cases disclose undercut, as the surface may really feel irregular or have a dip where the undercut exists.
Safety Nets for Undercut
Having a deep understanding of the causes of undercut in welds permits for the execution of reliable preventive procedures to keep weld quality and integrity. These settings should be enhanced to protect against excessive heat input, which can lead to undercut Home Page development.

Techniques for Dealing With Undercut

To resolve undercut issues successfully, welders can utilize specific methods aimed at fixing the flaw and restoring the integrity of the weld joint. One method is to adjust the welding criteria, such as the voltage, present, and travel rate, to ensure correct heat input and blend. Increasing the welding existing or minimizing the traveling speed can help fill out the undercut. Furthermore, changing the welding method from a push to a drag or vice versa can also aid reduce undercut.
Another method is to make use of a weaving motion while welding to guarantee proper sidewall blend and fill in the undercut. By oscillating the welding arc back and forth within the weld joint, the welder can transfer a lot more filler material right into the undercut locations, successfully getting rid of the defect.
Furthermore, grinding out the undercut and rewelding the joint can be a sensible remedy for a lot more severe undercut problems - Preventing weld undercut. This process entails removing the undercut section, preparing the site link base steel, and after that rewelding the joint with proper welding parameters and methods to avoid undercut from reoccurring
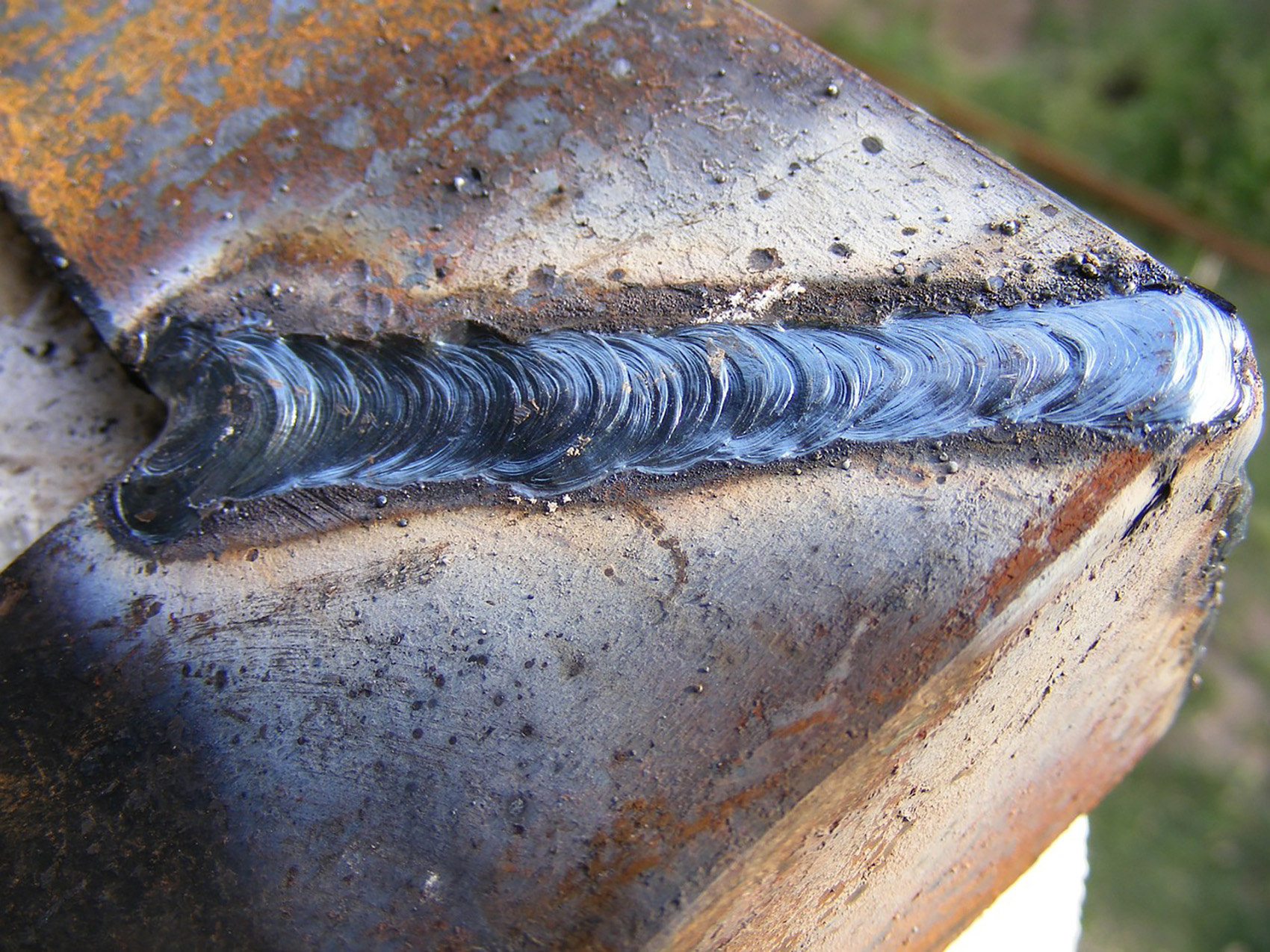
Specialist Tips for Staying Clear Of Undercut
Making use of appropriate welding methods and keeping control over vital welding parameters are crucial approaches for welders aiming to stop undercut in their weld joints. In addition, picking the ideal welding procedure and filler metal for the certain application can help avoid undercut. Preserving a regular traveling rate throughout the welding procedure is another vital idea to prevent undercut.
Verdict
To conclude, determining, preventing, and repairing undercut welding problems in your welding jobs is vital for making certain strong and resilient welds. Preventing weld undercut. By understanding the usual sources of undercut, having the ability to recognize it in welds, applying safety nets, and making use of appropriate methods for dealing with undercut, you can stay clear of potential concerns and create high-grade welds. Adhering to specialist pointers for avoiding undercut can assist you enhance your welding skills and create far better cause your jobs
Undercut welding, a typical issue in welding processes, can be triggered by various variables that need to be meticulously identified and resolved to guarantee the honesty of the weld joint. Additionally, running a finger or a finger nail along the weld joint can occasionally reveal undercut, as the surface might review feel irregular or have a dip where the undercut exists.
Using proper welding strategies and preserving control over crucial welding parameters are crucial methods for welders intending to avoid undercut in their weld joints.In final thought, recognizing, avoiding, and taking care of undercut welding troubles in your welding projects is important for ensuring durable and solid welds. By comprehending the typical causes of undercut, being able to recognize it in welds, applying preventative steps, and utilizing appropriate techniques for taking care of undercut, you can stay clear of possible concerns and produce premium welds.
Comments on “Best Overview to Preventing Weld Undercut: Tips and Techniques”